親和精工株式会社は、50年以上にわたり自動車用プラスチック部品の製造を手がけてきた老舗企業です。成形から検査・組立まで一貫した製造体制と、安定した品質で電気部品業界を支え続けてきました。しかし近年、物価高騰や社会環境の変化により、従来の生産管理方法では対応しきれない課題が顕在化。これを打開すべく、社内にプロジェクトを立ち上げ、専門家の助言を受けながら合理化・生産性向上に向けた取り組みを始めました。
どのような相談をしましたか?
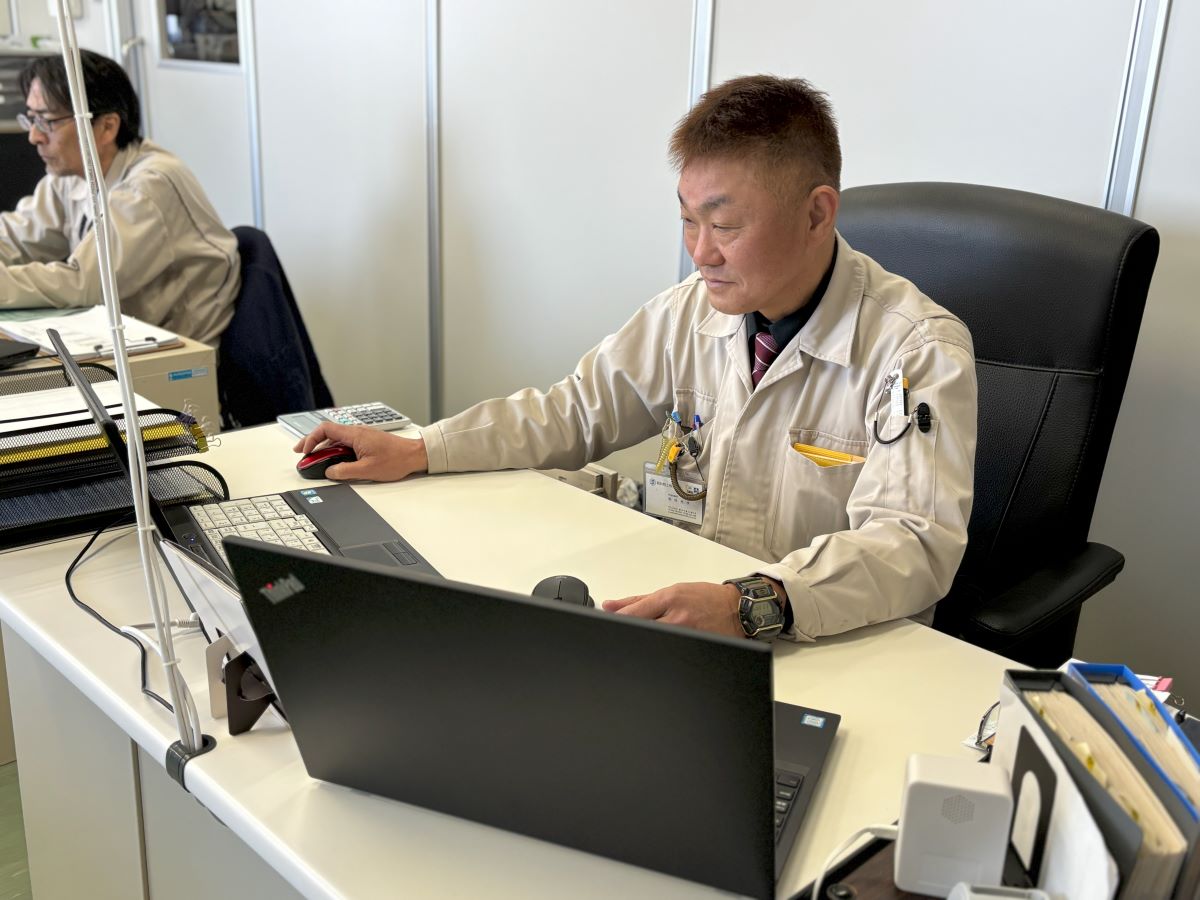
ここ数年の物価高騰は、当社のような製造業にとって大きな打撃でした。これまでと同じように製品を作っていては利益が確保できない状況となり、どこかで抜本的な改革が必要だという認識が社内でも広がっていました。
私たちは、長年にわたり同じやり方で生産管理を続けてきましたが、実態と合わない工数や加工時間がそのまま基準として使われているなど、実情にそぐわない部分が多々ありました。
どこをどう見直すべきか、現場を巻き込んだ形での改善が必要だと感じ、専門家に相談することにしたのです。
どのような助言を受けましたか?
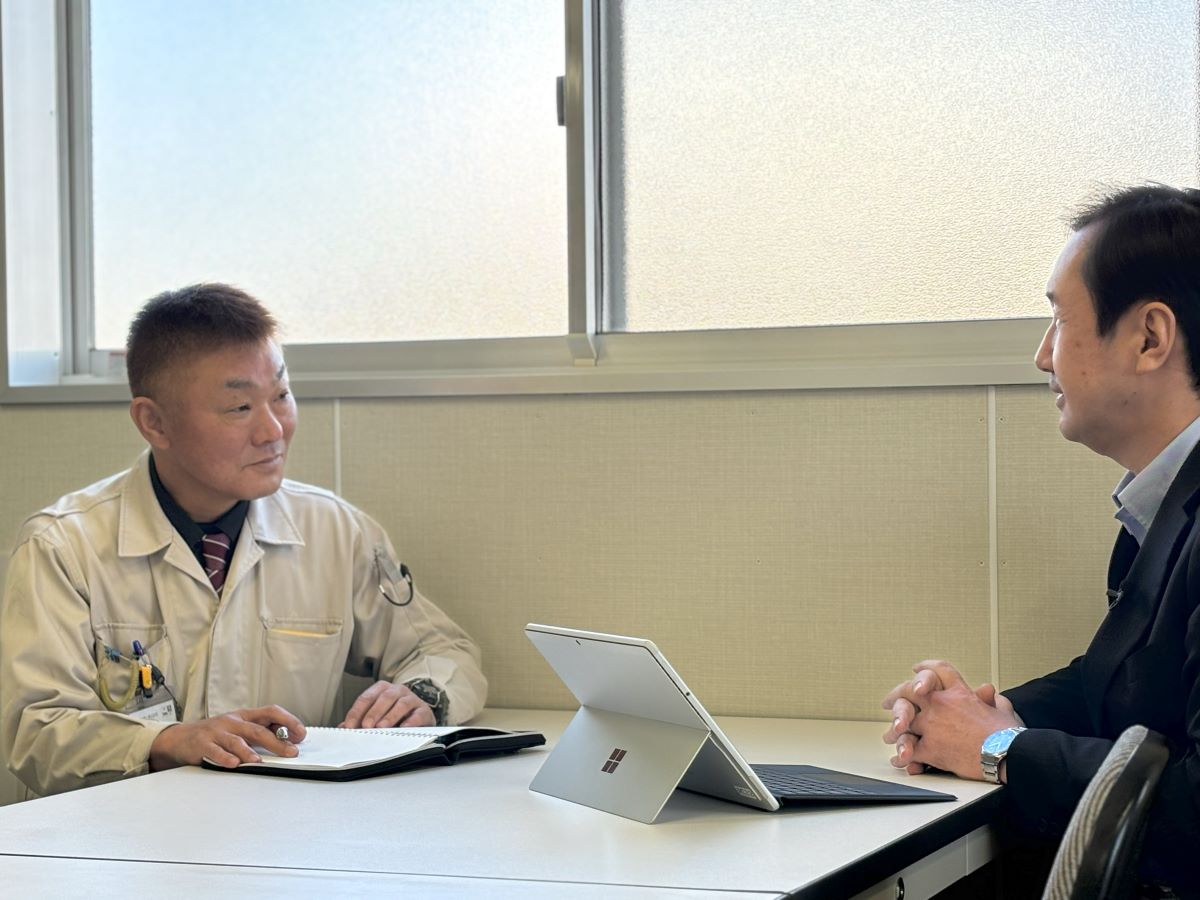
まず専門家から提案されたのは、「チームで改善に取り組む」という視点でした。トップダウンではなく、現場の意見を反映しながら進めることが、改革を浸透させる鍵だと助言されました。
具体的には、社内で生産性向上プロジェクトを立ち上げ、各工程の詳細な作業内容を見直し、ムリ・ムダ・ムラを洗い出すこと。そして、加工や組立にかかる実際の時間や工程を把握し、基準値と乖離している部分を明確にすることが求められました。
また、経費の計算方法についても再点検が必要との指摘を受け、新たな計算方法の習得と、それを踏まえた材料費や工程費の見直しにも取り組むようアドバイスを受けました。
改善提案を受けて何をしましたか?
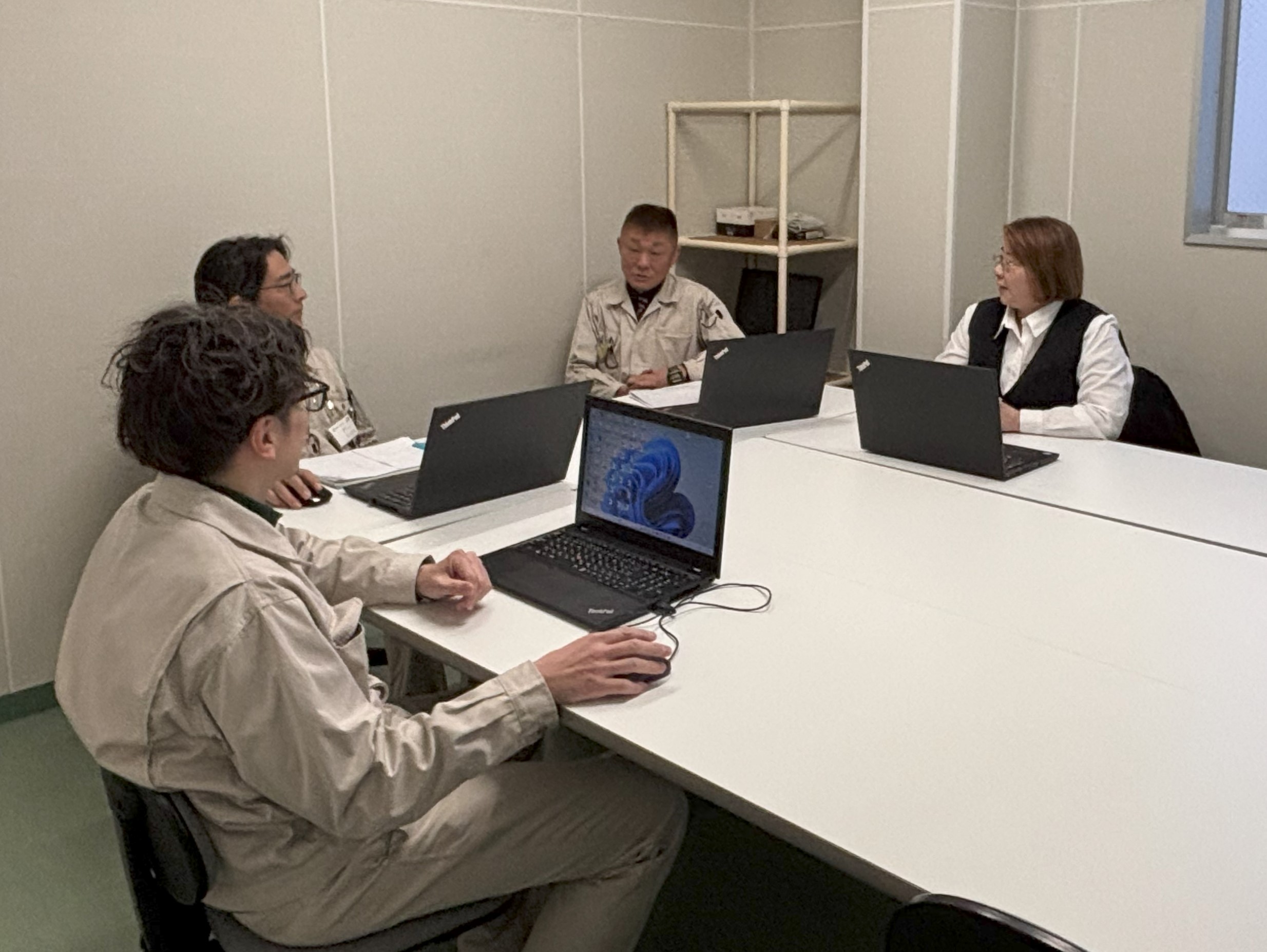
まずは社内にプロジェクトチームを設け、現場スタッフとともに「見える化」に着手しました。どの作業がどれだけの時間を要し、どこにムダがあるのかを数値で可視化し、それをベースに改善ポイントを明確化しました。
また、各工程の作業内容を再確認し、実態と合っていない基準工数を一つずつ修正していきました。その結果、工程ごとの改善箇所がはっきりと見え、重点的に対応すべき領域に集中して取り組むことができました。
加えて、作業のムリ・ムダ・ムラを徹底的に削減したことで、業務全体がより効率的に回るようになりました。このように作業工程が明確になったことにより、作業者の多能化も進めやすくなり、少人数でも安定した生産体制を構築できるようになりました。
支援を受けてどのように変わりましたか?
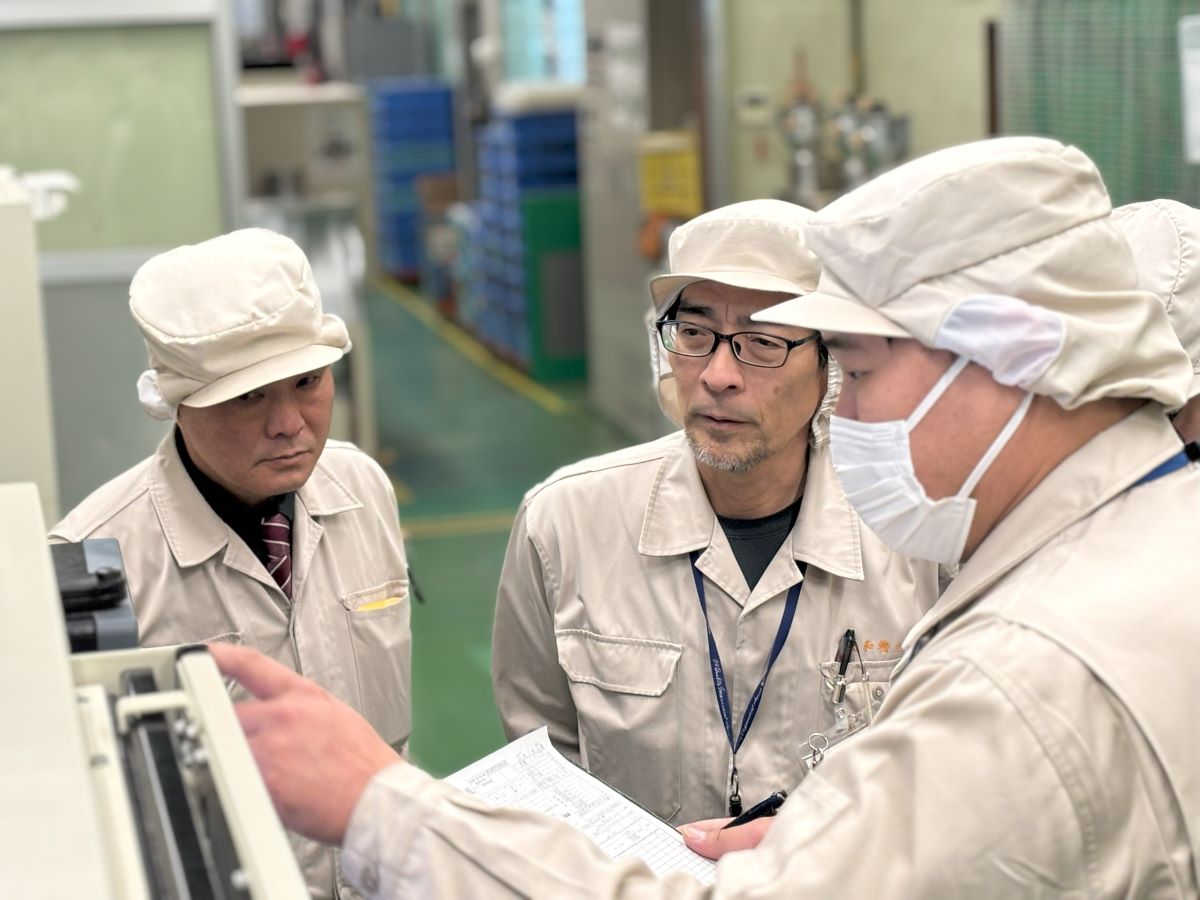
今回の取り組みを通じて、生産性が着実に向上しました。品質を維持したまま、工程や検査の効率が大幅に改善されたことで、無理なく安定した生産を維持できる体制が整いました。
なにより、従業員全体で改善に取り組んだことによる一体感が生まれたことが大きな成果です。見える化によって改善の効果が数値で見えるようになったため、従業員自身も手応えを感じられ、モチベーションの向上にもつながりました。
私自身も、今回の改革を通じて「人は年をとるものだが、会社は年をとってはいけない」という言葉を強く実感しました。変化に適応し続けるためには、日々改善していく姿勢が不可欠であることを改めて認識しました。今回の改革は、その第一歩となる貴重な機会だったと思っています。
行動計画
プロジェクトチームの立ち上げ
管理会計の導入・改善- あらためて各工程の時間や工数を把握することで、各工程のムリ・ムダ・ムラを洗い出し、生産性向上を図る
- 生産性向上プロジェクトを立ち上げ、全社的に合理化に取り組む体制を構築する。トップダウンではなく、現場スタッフとともに各工程作業時間等の「見える化」を実施し、合理化を進める